Are you searching for manufacturing solutions that reduce costs, minimise waste, and offer unparalleled design flexibility?
For New Zealand manufacturers, the debate between 3D printing and traditional manufacturing is more relevant than ever.
This article dives into the strengths, weaknesses, and real-world applications of both production methods to guide your next manufacturing decision.
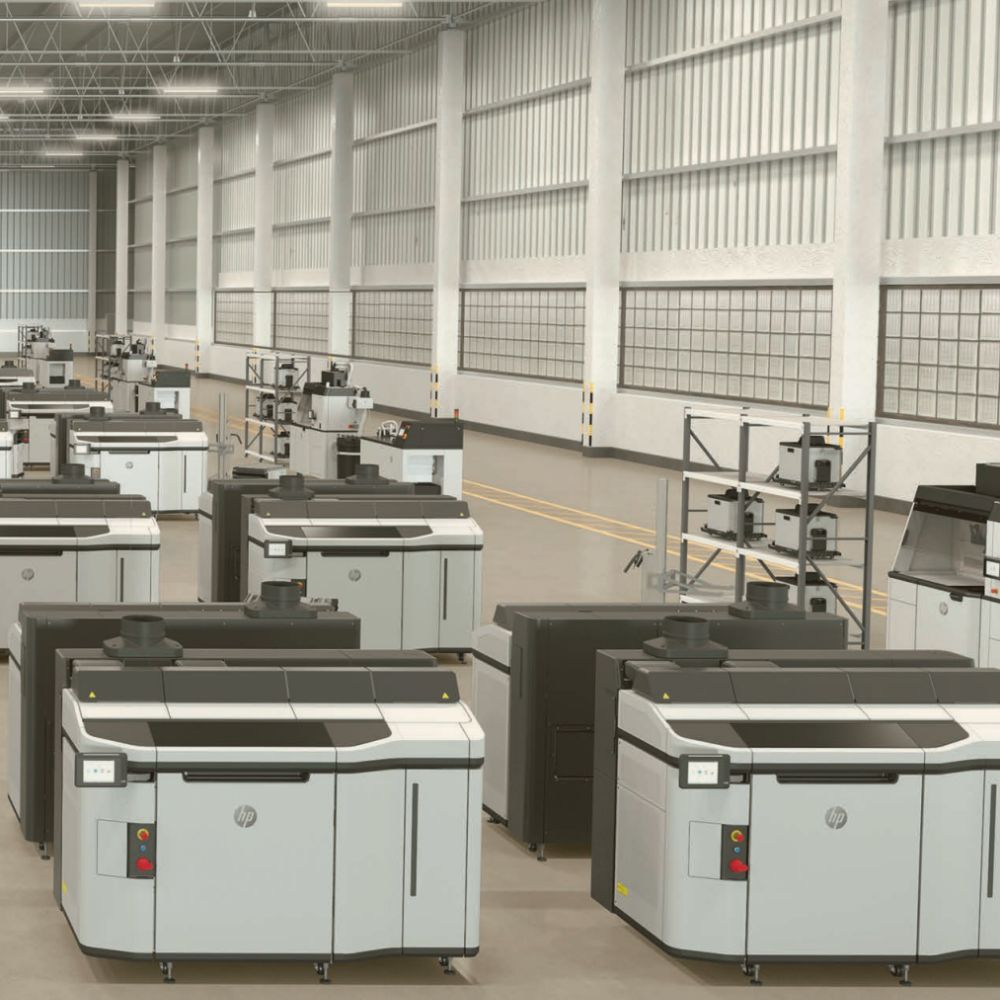
3d printing
3D Printing Vs Traditional Manufacturing
What is 3D Printing?
3D printing, or additive manufacturing, is a revolutionary production process where objects are created layer by layer from digital designs. It’s renowned for its ability to produce complex, customised designs efficiently. This method has found its place in industries like aerospace, healthcare, and fashion, particularly for prototyping and small-scale production.
What is Traditional Manufacturing?
Traditional manufacturing, often referred to as subtractive manufacturing, encompasses established methods such as injection moulding, CNC machining, and casting. These techniques excel at large-scale production and provide consistent quality but typically require higher upfront costs for tooling and setup.
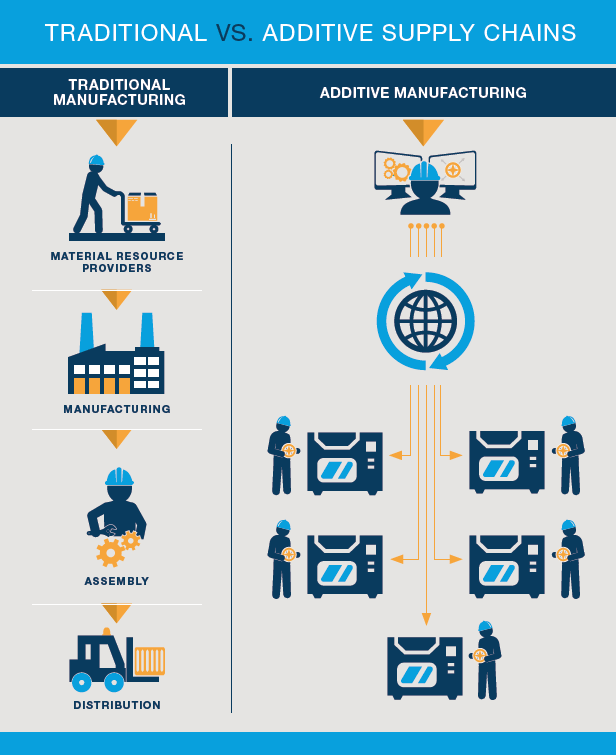
source: proto3000.com
6 Key Factors to Consider Between 3D Printing and Traditional Manufacturing
When deciding between 3D Printing and Traditional Manufacturing, understanding the key differences can help manufacturers make the best choice for their needs. Below are the five most important factors to consider:
1. Cost Efficiency
- 3D Printing: Perfect for small production runs and prototypes due to its low upfront costs. No need for expensive moulds or tooling, making it a cost-effective choice for custom designs.
- Traditional Manufacturing: While initial costs are higher because of tooling requirements, it becomes more economical for large-scale production thanks to economies of scale.
2. Customisation
- 3D Printing: Offers unmatched ability to create bespoke, intricate designs without additional tooling costs. It’s a go-to solution for industries like healthcare, fashion, and aerospace where personalisation is critical.
- Traditional Manufacturing: Best for standardised production. Customisation is possible but incurs higher costs and longer lead times due to tooling adjustments.
3. Production Volume
- 3D Printing: Ideal for low to medium production volumes or one-off, highly customised projects. It excels in offering flexibility for short-term manufacturing needs.
- Traditional Manufacturing: Tailored for high-volume production where consistency and efficiency are paramount. Best for long production runs with repetitive designs.
4. Design Flexibility
- 3D Printing: Enables the creation of intricate and complex designs that traditional methods can’t achieve, all without additional tooling costs. Perfect for creative and highly detailed projects.
- Traditional Manufacturing: Works best for standardised, repeatable designs due to tooling and machinery limitations, making it a great option for streamlined production.
5. Material Waste
- 3D Printing: Known for its sustainable approach, 3D printing uses only the material required for the design, significantly reducing waste.
- Traditional Manufacturing: A subtractive process that often results in high levels of material waste, especially in methods like CNC machining.
6. Speed and Lead Time
- 3D Printing: Offers faster turnaround times for prototyping and small-batch production, making it a go-to option for agile product development.
- Traditional Manufacturing: Requires longer lead times for tooling and setup, which can delay the start of production but becomes highly efficient once mass production begins.
Factor | 3D Printing | Traditional Manufacturing |
Cost | Low upfront costs; ideal for small runs. | High setup costs; better for large volumes. |
Volume | Best for small to medium production. | Efficient for high-volume production. |
Design | Unlimited flexibility for complex designs. | Limited by tooling and machinery. |
Waste | Minimal material waste (additive process). | Significant waste (subtractive process). |
Speed | Quick for prototyping and small batches. | Longer setup; efficient for mass production. |
Choosing the Right Method for Your Business
When deciding between 3D printing and traditional manufacturing, consider the following:
- Volume: Choose traditional manufacturing for high-volume production; opt for 3D printing for small batches or prototypes.
- Complexity: Use 3D printing for intricate or customised designs, while traditional methods work best for standardised items.
- Cost: Evaluate the initial investment versus long-term production requirements to determine the most cost-effective approach.
Real-World Applications in New Zealand Manufacturing
3D Printing in Action:
3D printing is driving innovation across various industries in New Zealand:
- Healthcare: Custom prosthetics and implants tailored to individual patients are transforming patient care, providing solutions that are both cost-effective and highly personalised.
- Aerospace: Lightweight components optimised for fuel efficiency are helping to reduce environmental impact, a growing priority for New Zealand’s aerospace industry.
- Fashion: Designers leverage 3D printing for intricate jewellery and accessories, creating bespoke items that are highly sought after in New Zealand’s creative industries.
- Agriculture: New Zealand’s agricultural sector is exploring 3D printing for customised tools, parts, and even equipment repairs, helping farmers adapt to specific needs without the high cost of traditional manufacturing.
Traditional Manufacturing in Action:
Traditional manufacturing remains vital for mass production in New Zealand:
- Automotive: High-volume production of durable components like engine parts keeps the local automotive sector running smoothly and efficiently.
- Consumer Goods: Everyday products, such as plastic bottles, are produced in large quantities using traditional methods, ensuring affordability and consistency.
- Construction: Prefabricated parts for infrastructure projects streamline building processes, meeting the growing demand for housing and commercial development.
- Renewable Energy: New Zealand’s renewable energy industry relies on traditional manufacturing for durable wind turbine components and other large-scale energy solutions critical to the country’s sustainability goals.
The Future: Combining Both Approaches
Many industries are leveraging the strengths of both methods. For example, companies may use 3D printing for prototyping or small-scale production before transitioning to traditional methods for mass production. This hybrid approach enables cost savings, innovation, and scalability.
The choice between 3D printing and traditional manufacturing depends on your specific needs, including production volume, design complexity, material requirements, and budget. Both methods offer unique advantages, and in many cases, a combination of the two can deliver optimal results. By understanding the strengths and limitations of each approach, New Zealand manufacturers can make informed decisions that enhance efficiency, reduce costs, and drive innovation.
Curious about which method suits your business? Contact us for a tailored consultation today.3D Printing vs Traditional Manufacturing: Which is Better for NZ Manufacturers 2024?
Are you searching for manufacturing methods that reduce costs, minimise waste, and offer unparalleled design freedom?
For New Zealand’s manufacturing industry, the debate between 3D printing vs traditional manufacturing is more relevant than ever.
This article explores the strengths, weaknesses, and advantages and disadvantages of 3D printing and traditional manufacturing to guide your next production process decision.
What is 3D Printing?
3D printing, or additive manufacturing, is an innovative manufacturing process where objects are created layer by layer from digital designs. Known for its ability to produce complex, customised designs efficiently, it’s a game-changer for industries like aerospace, healthcare, and fashion. This 3D printing technology is particularly effective for prototyping and small-scale production runs.
What is Traditional Manufacturing?
Traditional manufacturing, also called subtractive manufacturing, includes well-established manufacturing methods such as injection moulding, CNC machining, and casting. These traditional manufacturing processes excel in large-scale production where consistency and efficiency are key.
However, traditional manufacturing processes make high initial tooling costs a barrier for smaller projects. Products produced using traditional methods tend to have limited design flexibility compared to 3D printing.
source: proto3000.com
6 Key Factors to Consider Between 3D Printing and Traditional Manufacturing
When deciding between 3D printing and traditional manufacturing, understanding the differences between 3D printing and traditional production is crucial. Below are the six most important factors:
1. Cost Efficiency
- 3D Printing: Ideal for small production runs, prototypes, and customisation, with low initial costs. Calculating the cost of 3D printing reveals savings in tooling and material usage compared to traditional manufacturing.
- Traditional Manufacturing: While the cost of 3D printing is low for custom designs, traditional manufacturing methods tend to be more economical for mass production due to economies of scale.
2. Customisation
- 3D Printing: Enables manufacturing complex designs without the need for expensive tooling. 3D printing enables intricate, personalised creations at a fraction of the cost compared to traditional methods.
- Traditional Manufacturing: Limited customisation options that are often costly and time-intensive using traditional methods.
3. Production Volume
- 3D Printing: Best suited for low-volume production or highly customised projects. 3D printed parts are ideal for agile product development.
- Traditional Manufacturing: Highly efficient for large-scale production, with consistent quality. Manufacturing processes like injection moulding are commonly used for repetitive designs.
4. Design Flexibility
- 3D Printing: Offers unmatched flexibility of 3D printing, allowing for complex and innovative designs that many traditional manufacturing methods cannot achieve.
- Traditional Manufacturing: Restricted to standardised, repeatable designs, making it less suitable for bespoke projects.
5. Material Waste
- 3D Printing: Sustainable, with minimal material waste. Additive manufacturing eliminates the excess material that subtractive manufacturing methods often discard.
- Traditional Manufacturing: Significant waste is generated during traditional manufacturing processes, impacting sustainability.
6. Speed and Lead Time
- 3D Printing: Faster for small batches and prototypes, making it a preferred choice for companies seeking quick turnaround times. 3D printing is often faster than traditional methods.
- Traditional Manufacturing: Longer lead times for tooling and setup but highly efficient once production is underway. Faster than traditional manufacturing for large production runs.
Factor | 3D Printing | Traditional Manufacturing |
---|---|---|
Cost Efficiency | ✔ Low upfront costs; ideal for small runs and prototypes. | ✘ High initial investment; cost-effective for large-scale production. |
Customisation | ✔ Unlimited flexibility for intricate and bespoke designs without extra costs. | ✘ Limited; costly and time-consuming for customisation. |
Production Volume | ✔ Best for small to medium runs or on-demand manufacturing. | ✔ Highly efficient for mass production with consistent quality. |
Design Flexibility | ✔ Supports complex, innovative designs easily. | ✘ Restricted to standardised designs due to tooling constraints. |
Speed and Lead Time | ✔ Rapid prototyping and shorter lead times for small batches. | ✘ Longer lead times; efficient once setup is complete for large runs. |
Material Waste | ✔ Minimal waste; uses only the necessary material. | ✘ High waste; subtractive methods discard excess material. |
Environmental Impact | ✔ Sustainable; low material waste and often recyclable materials. | ✘ Higher environmental impact due to waste and energy consumption. |
Choosing the Right Method for Your Business
When deciding between 3D printing and traditional manufacturing, consider the following:
- Volume: Choose traditional manufacturing for high-volume production; opt for 3D printing for small batches or prototypes.
- Complexity: Use 3D printing for intricate or customised designs, while traditional methods work best for standardised items.
- Cost: Evaluate the initial investment versus long-term production requirements to determine the most cost-effective approach.
Real-World Applications in NZ Manufacturing
3D Printing in Action
- Healthcare: 3D printed parts such as prosthetics and implants are transforming patient care with cost-effective, personalised solutions.
- Aerospace: Lightweight components reduce environmental impact while supporting innovation in the sector.
- Agriculture: Customised tools and equipment repairs demonstrate how using 3D printing benefits the industry.
Traditional Manufacturing in Action
- Automotive: High-volume production of durable components ensures reliability and efficiency.
- Consumer Goods: Everyday products like plastic bottles are mass-produced affordably and consistently.
- Construction: Prefabricated components streamline infrastructure projects and meet growing demand.
Choosing between 3D printing over traditional manufacturing depends on your business needs. For bespoke, low-volume production, 3D printing offers many advantages in cost, sustainability, and customisation. However, using traditional methods is more efficient for mass production.
For NZ manufacturers, a hybrid approach that leverages both 3D printing processes and traditional manufacturing techniques can offer the best of both worlds.
Curious about which method suits your business? Contact us for a tailored consultation today.